Mastering Quality Control for Superior Insulated Tumbler Manufacturing
Quality Control (QC) is vital in manufacturing high-quality insulated tumblers, ensuring customer sa…….
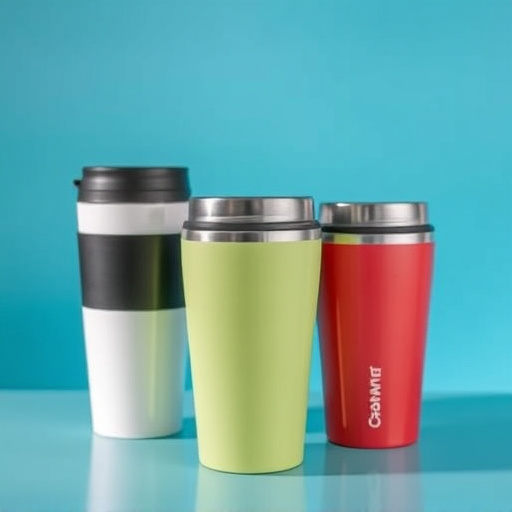
Quality Control (QC) is vital in manufacturing high-quality insulated tumblers, ensuring customer satisfaction through rigorous testing. This includes material defect inspection, dimensional verification, and performance tests like thermal insulation efficiency trials, drop tests, and aesthetic evaluations. Advanced technologies like temperature sensors aid in accurate assessments. Strict QC procedures guarantee each tumbler meets exact standards, providing consumers with a reliable drinking experience, extending product lifespans, and fostering brand trust in a competitive market.
Quality control is a cornerstone in the manufacturing process, especially for intricate products like insulated tumblers. This article delves into the critical role it plays in ensuring top-tier craftsmanship. We explore rigorous testing procedures essential for insulated tumblers, highlighting visual inspection and dimensional accuracy as key aspects. Additionally, we discuss how robust quality control enhances customer satisfaction and extends product lifespan—a vital consideration in today’s competitive market.
- Understanding Quality Control: The Role in Insulated Tumblers Manufacturing
- Implementing Rigorous Testing Procedures for Insulated Tumblers
- Visual Inspection and Dimensional Accuracy: Ensuring Every Detail Matters
- The Impact of Quality Control on Customer Satisfaction and Product Lifespan
Understanding Quality Control: The Role in Insulated Tumblers Manufacturing
In the manufacturing process of insulated tumblers, Quality Control (QC) plays a pivotal role in ensuring product excellence and customer satisfaction. It involves a series of rigorous checks and tests at every production stage to identify and rectify any deviations from the set quality standards. For insulated tumblers, this is particularly critical as maintaining thermal insulation properties, material integrity, and overall durability is paramount.
QC measures include inspecting materials for defects before processing, verifying dimensions and specifications throughout manufacturing, and conducting performance tests post-production. These tests may involve checking insulation efficiency through temperature retention trials, assessing structural integrity by drop or impact tests, and evaluating the overall aesthetic appeal and functionality of each tumbler. By implementing robust QC procedures, manufacturers can guarantee that every insulated tumbler meets high-quality standards, ensuring customer trust and fostering brand reputation in a highly competitive market.
Implementing Rigorous Testing Procedures for Insulated Tumblers
In the context of manufacturing and ensuring product excellence, implementing rigorous testing procedures is paramount, especially for complex items like insulated tumblers. These drinking vessels, designed to keep beverages hot or cold for extended periods, demand meticulous quality control measures. Testing should encompass a wide range of criteria, from thermal insulation efficiency to durability and leak-proofness under varying conditions.
Rigorous testing involves subjecting insulated tumblers to extreme temperatures, simulating real-world use scenarios, and conducting leak tests to ensure their integrity. Advanced technologies like temperature sensors and pressure systems can help assess performance accurately. By implementing these stringent procedures, manufacturers can guarantee that each tumbler meets high standards, providing consumers with a reliable and enjoyable drinking experience.
Visual Inspection and Dimensional Accuracy: Ensuring Every Detail Matters
Visual inspection and dimensional accuracy are paramount in maintaining quality control, especially for products like insulated tumblers where precision matters. Skilled inspectors meticulously examine each tumbler, checking for any visible defects such as scratches, chips, or irregularities on the surface. This meticulous process ensures that the exterior not only looks appealing but also provides a smooth finish, enhancing user experience.
Moreover, dimensional accuracy is crucial to guarantee that insulated tumblers meet specified size requirements. High-precision measuring tools are employed to verify critical dimensions, ensuring each tumbler adheres to stringent tolerances. This attention to detail prevents leaks and ensures the product’s effectiveness in maintaining desired temperatures for extended periods.
The Impact of Quality Control on Customer Satisfaction and Product Lifespan
Quality control plays a pivotal role in ensuring customer satisfaction and extending the lifespan of products, particularly in industries like insulated tumblers. By implementing rigorous quality checks at every production stage, manufacturers can identify and rectify defects or inconsistencies before the final product reaches consumers. This proactive approach significantly reduces the likelihood of customers encountering issues with their purchases, fostering trust and loyalty towards the brand.
For insulated tumblers, effective quality control measures ensure that products maintain their promised insulation properties, temperatures, and overall functionality. It prevents issues like leaking, rapid temperature loss, or structural failures, which could negatively impact user experience and product reputation. Consequently, high-quality insulated tumblers tend to enjoy longer lifespans, providing value for money and contributing to environmental sustainability by reducing the need for frequent replacements.
In the manufacturing process of insulated tumblers, quality control is not just a step but a commitment. By implementing rigorous testing procedures, visual inspection, and focusing on dimensional accuracy, manufacturers can ensure that each product meets high standards. This dedication to quality directly impacts customer satisfaction and product lifespan, fostering trust in the brand and encouraging repeat purchases. For insulated tumblers, where performance and longevity are paramount, robust quality control measures are a recipe for success in a competitive market.