Insulated Tumbler Production: Materials, Processes, and Market Trends
Insulated tumblers, designed for extended beverage temperature retention, leverage double-wall const…….
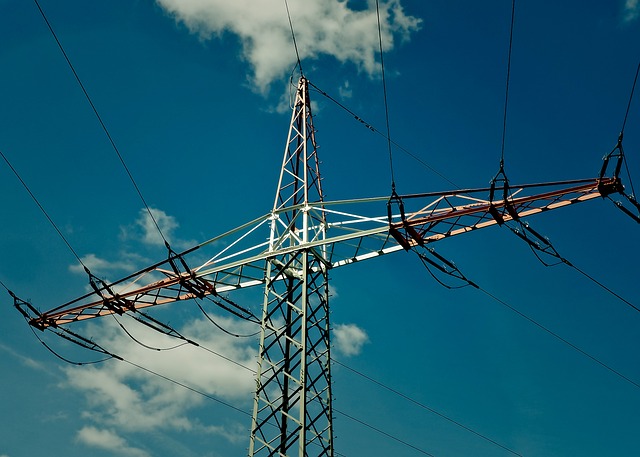
Insulated tumblers, designed for extended beverage temperature retention, leverage double-wall construction with air-insulated spaces from materials like stainless steel or aluminum. Advanced insulation techniques, including vacuum insulation, enhance thermal retention. Strict quality control measures ensure consistency and prevent defects. Sustainability practices use recycled materials and circular economy models to reduce environmental impact. Customization options cater to diverse tastes, while market trends drive innovation in materials and designs to meet consumer demands.
Insulated tumblers have transformed how we enjoy hot or cold beverages, offering unparalleled thermal retention for hours. This article delves into the intricate world of production methods behind these versatile vessels. From material selection and design innovation to insulation techniques and quality control measures, each step ensures superior performance. We explore sustainable practices, customization options, and market trends that are revolutionizing the way we produce and consume insulated tumblers, catering to diverse consumer preferences.
- Understanding Insulated Tumblers: Materials and Their Role
- Manufacturing Processes: From Design to Production
- The Art of Insulation: Techniques for Thermal Retention
- Quality Control Measures in Insulated Tumbler Production
- Sustainable Practices: Eco-Friendly Materials and Recycling
- Customization Options: Personalized Designs and Applications
- Market Trends and Consumer Preferences Shaping Production
Understanding Insulated Tumblers: Materials and Their Role
Insulated tumblers are designed to keep beverages at their desired temperature for extended periods, making them a popular choice for outdoor activities and daily use alike. The key to their effectiveness lies in the materials used in construction. Typically, these tumblers feature double walls with an air-insulated space between, ensuring heat retention or insulation. High-quality stainless steel or aluminum are common choices due to their durability, corrosion resistance, and ability to maintain temperature.
The role of these materials extends beyond structural integrity; they also contribute to the overall performance and user experience. Stainless steel, known for its strength and sanitation properties, is often used in food-grade applications. Aluminum, lighter and equally robust, offers excellent heat conductivity, enhancing the tumbler’s insulation capabilities. Additionally, some models incorporate vacuum insulation technology, further improving their temperature retention, making them the go-to option for those seeking maximum refreshment on-the-go with their favorite beverages.
Manufacturing Processes: From Design to Production
In the realm of manufacturing, the journey from design to production for items like insulated tumblers involves a meticulous process that ensures quality and efficiency. It all begins with conceptualization, where designers craft detailed plans, considering factors such as aesthetics, functionality, and material choices. This initial phase sets the foundation for the entire production run.
Once the designs are finalized, the manufacturing process kicks into gear. For insulated tumblers, production typically involves a combination of machining, molding, and assembly lines. Advanced machinery precisely cuts and shapes the materials, while specialized processes insulate the containers to maintain beverage temperature. Each step is carefully monitored to meet quality standards, ensuring that the final product not only looks great but also functions as intended, keeping drinks hot or cold for extended periods.
The Art of Insulation: Techniques for Thermal Retention
In the realm of production, the art of insulation plays a pivotal role in enhancing thermal retention, particularly in items like insulated tumblers. Advanced techniques are employed to create barriers that prevent heat transfer, ensuring beverages remain at their desired temperature for extended periods. These methods involve intricate processes, from selecting high-performance materials like stainless steel and vacuum insulation to implementing sophisticated fabrication strategies.
By combining scientific principles with craftsmanship, manufacturers develop innovative designs that trap air or use phase-change materials to absorb and retain heat. Such expertise not only contributes to the comfort of users but also aligns with today’s eco-conscious trends by reducing the need for frequent reheating or cooling, thereby promoting sustainability in everyday products like insulated tumblers.
Quality Control Measures in Insulated Tumbler Production
In the meticulous process of insulated tumbler production, Quality Control Measures (QCM) play a pivotal role in ensuring each product meets the highest standards. From raw material selection to final assembly, stringent protocols are implemented to maintain consistency and prevent defects. During manufacturing, visual inspections are conducted at various stages to identify any irregularities or deviations from the set specifications, guaranteeing that every insulated tumbler adheres to strict quality criteria.
Furthermore, advanced testing methods are employed to assess critical factors such as insulation effectiveness, durability, and overall performance. This includes leak testing to confirm the integrity of seals and thermal stability assessments to ensure the tumblers maintain desired temperature levels. By integrating these QCMs, manufacturers can deliver top-quality insulated tumblers that offer superior functionality, enhanced user experience, and lasting reliability.
Sustainable Practices: Eco-Friendly Materials and Recycling
In today’s eco-conscious landscape, sustainable practices are transforming the production methods of various industries, and the market for insulated tumblers is no exception. Manufacturers are increasingly adopting eco-friendly materials to create these reusable beverage containers, reducing their environmental footprint. By utilizing recycled plastic, stainless steel, or even plant-based bioplastics, producers can minimize waste and lower energy consumption associated with traditional manufacturing processes.
One notable aspect of this shift is the emphasis on recycling programs that extend beyond the product’s lifespan. Many brands now offer collection systems for used insulated tumblers, ensuring they are responsibly recycled or upcycled. This circular approach not only conserves resources but also reduces the amount of plastic ending up in landfills or entering natural ecosystems. As consumers become more aware of these practices, they can make informed choices, supporting companies that align with sustainable values and contribute to a greener future.
Customization Options: Personalized Designs and Applications
Customization options have transformed the way products are created, especially in industries like manufacturing and retail. When it comes to insulated tumblers, customers now demand personalized designs that cater to their unique preferences and needs. This shift towards customization allows businesses to offer a wide range of applications, from corporate branding to special occasions.
Insulated tumblers, for instance, can be tailored with custom artwork, text, or logos, making them ideal for promotional items or gifts. The use of advanced printing techniques enables intricate designs and vibrant colors, ensuring each tumbler is as unique as its owner. This level of personalization not only enhances customer satisfaction but also creates a lasting impression, making customized insulated tumblers a popular choice for those seeking to stand out in a crowded market.
Market Trends and Consumer Preferences Shaping Production
In today’s dynamic market, consumer preferences and trends play a pivotal role in shaping production methods, especially for products like insulated tumblers. The demand for sustainable and eco-friendly alternatives has led manufacturers to explore innovative materials and designs. For instance, the growing popularity of reusable insulated tumblers reflects a shift towards reducing single-use plastic waste. This trend not only influences manufacturing processes but also drives the adoption of advanced insulation technologies and durable, high-quality materials to ensure longevity and consumer satisfaction.
Moreover, the rise of online shopping and fast delivery expectations has prompted producers to optimize their supply chains and logistics. Consumer demands for quick access to products have resulted in more efficient production runs and agile inventory management systems. As insulated tumbler manufacturers adapt to these market trends, they must balance quality, innovation, and cost-effectiveness while meeting the evolving needs of discerning consumers.
Insulated tumblers have evolved beyond simple beverage containers, becoming a blend of art, science, and sustainable practices. From material selection and intricate insulation techniques to quality control and eco-friendly production methods, each step in the manufacturing process plays a critical role in delivering high-quality products that meet consumer demands. As market trends continue to favor personalized designs and sustainable solutions, the future of insulated tumbler production looks promising, with innovative technologies and responsible practices shaping the industry’s course.